陈荣生
贵州省某烧结砖企业生产空心砖和普通砖,原料为硬质页岩、软质页岩及黏土和原煤,设计年生产能力为6000万元(折标砖)空心砖,采用机械码坯、一次码烧工艺。干燥室和烧成隧道窑各2条,截面均为3.7m,干燥室长度为84.3m,烧成隧道窑长度为115m,窑车规格为3.7mX3.7m。
生产中,三组分原料按照比例预先混合后,共同通过锤式破碎机破碎、回转筛筛分,合格混合料进入生产线,双级真空挤出机成型,成型水分约14%,泥条经过自动切条切坯,每泥条切坯32块,机械码坯每次抓取12个泥条共384条,普通砖码高15层,窑车台面上码放9垛砖坯,每辆窑车码坯量达到5760块。根据烧成工艺要求,混合料内燃掺配量按照350kcal/kg的比例控制。烧结普通砖日产量到18~20万块。烧成隧道窑进车时间约为80min,烧成周期达到40~44h。
2014年8月,随着原料矿山开采条件的变化,软质页岩及黏土的成分出现波动,当按照固定的350kcal/kg的比例内燃值进行掺配时,在焙烧过程中,窑车中部部分产品出现膨胀变形和裂纹,断砖中部厚度达到68mm,砖顶面厚度达到55mm,成为“面包砖”,外观尺寸超出国家标准指标。生产一段时间后,此类膨胀和裂纹缺陷的普通砖数量达到30万块,对产品的质量评价造成不利影响。当降低内燃掺配后,砖垛中膨胀变形和裂纹产品数量基本消失。但是,在加强看火投煤情况下,在砖垛外侧下部,仍然出现欠货砖,详见图1~3。对此,就该企业烧结普通砖焙烧变形分析如下,供参考。
1 焙烧缺陷的产生
根据陶瓷烧结的定义,粉末或非致密性物料,经加热到低于其熔点的一定范围内,发生颗粒粘结,结构致密程度增加,晶粒长大,强度和化学稳定性提高等物理变化、成为坚实集合体的过程。
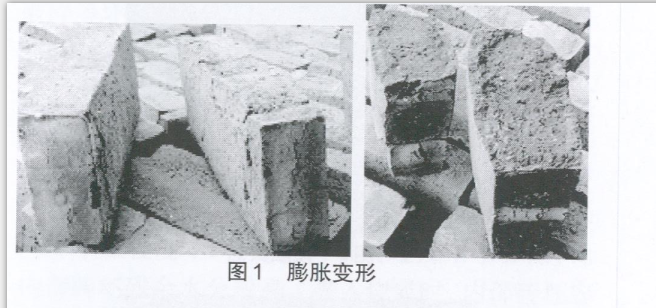
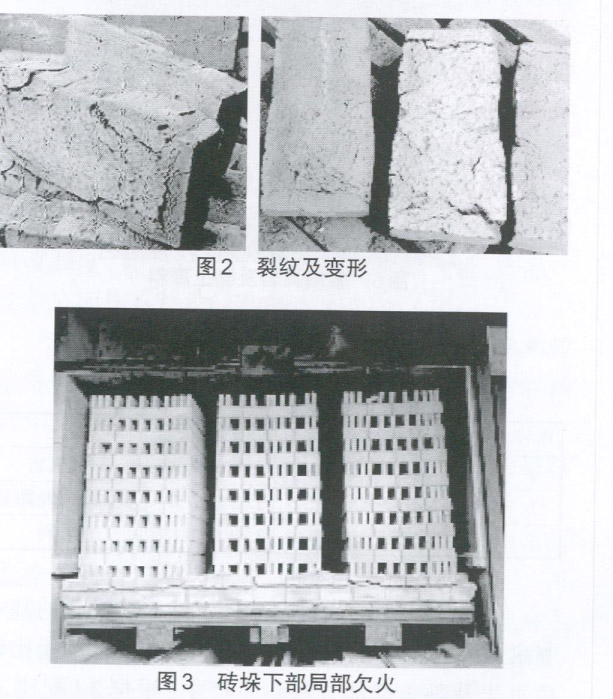
烧结砖坯体被加热后,由于混合料中氧化硅、氧化铝、氧化钙及氧化镁等金属氧化物的不同组成对混合料的最高烧结温度存在直接影响,使得其熔点范围加大,工艺控制难度增加。如果不能及时调整,焙烧过程中烧结砖产品极易出现收缩、膨胀、欠货、裂纹、断裂等现象,同时会跟随工艺调整交替产生,废品率增加。
1.1 原料成分的影响
该企业原料矿山采用挖掘机开采,由于开采条件限制,硬质页岩与软质页岩及黏土开采后,没有堆存风化等预处理措施,原料形态见图4、
5.
页岩性能比软质页岩及黏土与1份硬质页岩,内燃掺配量按照350kcal/kg的比例掺配。混合料成分中,溶剂成分Fe₂O₃、氧化镁、氧化钙略微偏高。隧道窑烧成过程中,焙烧带温度曲线显示,最高温度达到1000℃时,砖垛中部出现软化变形、膨胀和变形,如图1、2所示。
针对膨胀变形砖断面的分析,可见由砖坯表面到砖坯中心部位,断面颜色由浅红逐渐转变为浅灰,再由浅灰转为蓝黑。这是砖坯表面燃料煤处于氧化气氛下燃烧时,砖坯成分中Fe₂O₃没有分解,使得砖坯表面呈浅红色。随着氧化气氛减弱,Fe₂O₃逐渐分解,颜色逐渐转变为浅灰,到达砖坯中心时,由于空气中氧气无法进入,砖坯内燃煤处于还原气氛下燃烧,Fe₂O₃分解为4FeO和2CO2,正是因为FeO呈色为蓝灰到蓝黑,使得砖坯断面中心部位呈色与FeO呈色一致。
此外,当隧道窑窑温曲线显示为1000℃时,窑车中部砖垛内温度将达到或超过1000℃,砖坯内液相产生,气孔减少,并逐渐软化,砖坯内部的还原气氛使得Fe₂O₃分解,促使CO2气体排放,砖坯出现膨胀、裂纹和变形等缺陷。
正是由于砖坯内Fe₂O₃、MgO、CaO等溶剂成分的作用,使得砖坯在低于其熔点以下的烧结温度控制难度较大,同时由于码垛方式的限制,隧道窑全截面的温度差异较大。当按照固定的内燃掺配比例安排生产时,砖垛边部烧结温度适中,中部烧结温度出现偏高,产生焙烧膨胀、裂纹等变形缺陷。
1.2 配料及内燃掺配的影响
由于砖垛中部砖坯膨胀变形,该企业决定调整原料配比,采用1份软式页岩及黏土与1份硬质页岩,提高硬质页岩掺配,内燃掺配量按照320kcal/kg的比例掺配。同时要求烧成隧道窑岗位工加强对边火温度的观察,加强投煤。调整原料配比和内燃后,隧道窑窑温曲线控制为1030℃。
调整后,窑车中部砖垛砖坯膨胀变形想象基本消失,然而,窑车砖垛外侧下部出现欠火砖,如图3所示。膨胀变形消失的因素分析如下。
原料配比调整后,硬质页岩掺配量提高,高温难熔氧化物SiO2含量增加,对提高砖坯烧结温度、减少高温变形有利。
硬质页岩破碎后,欧体内颗粒较粗,有利氧气对坯体的渗透,减少还原气氛对Fe₂O₃分解。同时,坯体内粗颗粒之间的间隙有利于氧化和还原反应的产生气体的排出,能够有效地避免坯体的膨胀变形。
软质原料减少后,混合料中黏土微小颗粒减少,能够提高砖坯内产生液相度,避免坯体软化变形。
采用原煤内燃掺配的焙烧工艺,坯体内部必然形成还原气氛焙烧,无法避免。减少内燃掺配的控制措施,能够避免砖垛中部阻力高、烟气流速慢带来的砖垛内温度过高现象,减少隧道窑高温带截面温度差异过大,同时,随着砖坯内碳量降低,还原气氛减弱,减少Fe₂O₃分解和CO2气体排放,避免砖坯软化和膨胀、裂纹、断砖等焙烧缺陷的产生。
生产中,由于硬质页岩掺量提高,砖坯的烧成温度相应需要提高,在减少内燃掺配的条件下,企业强调烧窑工加强对边火温度的观察和投煤,要求控制窑温为1030℃,满足焙烧工艺要求。但由于边部投煤孔位置、砖垛与窑墙间隙基本固定,调整难度较大,两侧边火火行速度较快,火不易下底,造成窑车砖垛外侧下部出现欠火砖。加大边部投煤后,煤的不完全燃烧现象增加,燃料消耗提高。
1.3 机械码坯的限制
该企业采用机械码坯,3.7mX3.7m窑车每次码放1层,分成9垛,共码放15层。
生产中,需要根据原料性能、湿坯规格、投煤孔分布、码窑方式等参数,按照焙烧工艺要求确定机械码坯夹具位置。砖垛形式一般满足“边密中稀、上密下稀”的码放方式。夹具位置较少变动。
然而,在生产过程中经常出现原料性能和内燃掺配的波动和调整,此时,需要调整砖垛的码坯形式,以适应焙烧的需要,但机械码坯夹具位置的调整需要经验丰富的技术工人和一定时间来操作,而生产班员工往往不等夹具位置的调整,仍然按照工艺条件变化前的方式码坯,使得焙烧过程中产品出现较多焙烧缺陷。此种情况下,如仍然按照生产计划安排进车时间,对烧成周期不加控制,焙烧缺陷将越来越严重,废品率大幅度提高。这也是采用降低内燃掺配后砖垛下部出现局部欠火缺陷的原因。
1.4 成型水分的影响
企业采用55型双级真空挤出机成型,下级电动机功率为160kw,天气条件较好时,能够保持成型水分14%,泥条外观质量较好,满足机械码坯的需要。目前矿山还未拓展开来,因而软质原料受雨天的影响,自然含水率有波动,使得配料准确性发生变化,当成型水分达到16%时,湿坯在干燥室内往往产生干燥裂纹,焙烧过程中裂纹扩展,形成焙烧缺陷。
2 避免焙烧缺陷的措施
焙烧缺陷的产生,主要原因在于原料性能、掺配比例,应采取如下措施避免,
2.1 调整原料配比
根据原料性能,增加硬质页岩的掺配比例,使得混合料中高温难熔氧化物SiO2和Al2O3含量提高,从而提高烧结温度范围。随着硬质原料的加入,破碎筛分后混合料颗粒级配更为合理,但塑性指数将有所降低,此时需要低成型水分挤出成型,提高双级真空挤出机挤出压力,以获得质量较好的泥条,保证湿坯强度及外观尺寸要求,在后续工艺环节中减少干燥缺陷,调焙烧质量。
在生产中调整原料配比的措施,是减少和避免烧成缺陷的主要手段,需要在矿山开采、硬质原料破碎等环节做好准备。
2.2 准确与稳定的内燃掺配
干燥焙烧的工艺中,由于砖垛在窑内的码放方式限制,砖垛内外阻力不同,烟气流速存在差异,引起砖垛内外温度差异。
干燥过程中,砖垛内部烟气流速慢,使得砖垛内外干燥程度不同,砖垛外部砖坯残余水分低,而内部砖坯残余水分较高。进入烧成时,内部砖坯容易产生裂纹。
焙烧过程中,砖垛内部阻力大,烟气流速慢,使得砖垛内外温度存下差异,砖垛内部温度偏高,坯体容易出现粘结和变形。
鉴于以上因素,对于一次码烧工艺来说,内燃掺配量的准确与稳定是干燥和焙烧的基本保证,对烧成制度、烧成稳定性、烟气温度和烟气量、产品产量等方面均有较大的影响。
首先,需要根据内燃料的发热量、含水率和粒度等性能参数,通过生产实践,制定适宜的内燃掺配比例,为准确掺配内燃料创造条件。
其次,采用性能可靠的计量设备,保证内燃料的准确稳定。
第三,结合内燃程度,制定烧成隧道窑自动窑温控制曲线,同时以此为依据,规定烧窑岗位工操作原则。在自动检测窑温辅助条件下,加强烧窑工对窑温的调整和控制。
2.3 加些码坯夹具位置调整
正是因为砖垛在窑内的码放方式限制,使得干燥和焙烧存在残余水分和温度方面的差异,带来产品缺陷。即便通过原料配比和内燃掺配调整控制效果仍未满足要求时,则需要调整机械码坯夹具位置,按照“边密中稀、上密下稀”的方式,砖垛距隧道窑直墙间距要小,砖垛中部通风顺畅,选择更加适合的码坯方式。
按照现有窑车台面上码放9垛砖坯的方式,隧道窑正截面上,每砖垛长宽规格为1Mx1M
,3垛三列,窑车纵横向上分别有4条风道,正截面平均风道宽度为175密码,窑车上砖垛中部无风道。
如将加些码坯夹具位置进行调整,窑车台面上码放16垛砖坯,每砖垛长宽规格为750mmX750mm,4垛4列,码坯容量不变。横向上风道为5条,窑车正截面上有5条风道,正截面平均宽度为140mm,窑车上砖垛中部有风道。
调整后,隧道窑正截面风道数量增加,平均宽度减小,窑车上砖垛中部风道对要界面温度的均匀性有利。同时,砖垛规格变小,干燥过程中,砖垛内外砖坯热交换较为均匀,干燥程度一致,参与水分差异降低,进入烧成隧道窑后,砖垛内外坯体温差缩小,砖垛中部不会形成高温变形,全窑范围内温度和焙烧过程容易控制,能够有效地减少中部砖坯高温变形的产生。
2.4 严格控制成型水分
一次码烧工艺中,成型水分较高时,当湿坯码坯高度为15层,下部湿坯易出现变形,且砖垛中部水分不易排出。进入烧成隧道窑后,变形和缺陷扩大。此外,成型水分较高,如不能及时提高排潮速度,同样会因为水蒸气冷凝结露,冷凝水吸附或滴落在砖坯上,造成砖坯变形和开裂。
一次码烧工艺在雨天等不利条件生产时,只能采用延长窑车进车时间,及时调整烧成周期的方式,避免焙烧缺陷。
3 结束语
机械码坯的一次码烧工艺,焙烧缺陷的产生与原料性能相关性较高。工艺中内燃掺配、成型水分、混合料陈化、码坯方式、隧道窑结构和保温等均对焙烧质量影响较大,当明确影响因素后,提出调整措施。生产中,由于工艺及隧道窑结构条件均已确定,分别对焙烧变形现象以及配比调整后出现局部欠火、煤耗增加现象进行分析,对比其效果后,决定采用提高硬质页岩掺配比例,维持原有内燃掺配量不变的调整措施,能够完成日产18~20万块普通砖生产计划。
本文摘自:《砖瓦》
相关文章
- 2024-04-14菏泽市电力设备的一个强势品牌
- 2024-04-14电力电工解决方案的服务商
- 2024-04-14山东鸿盛电气科技有限公司
- 2024-04-09【鸿盛HONGSHENG,主要经营范围】
- 2024-04-09【鸿盛HONGSHENG,一个高端电力设备的品牌】
- 2024-04-09鸿盛电气的优势
- 2024-04-09鸿盛电气发展历程
- 2024-04-09鸿盛电气企业文化
- 2024-04-09鸿盛电气由“产品经营”走向“品牌经营”
- 2024-04-09鸿盛电气企业定位