摘要:介绍砖坯水分存在形式和干燥原理,总结生产实践中干燥工艺特点,给出了新建中大断面隧道窑应在干燥工艺设计方面注意的要点。
关键词:排潮;隧道窑;干燥敏感性;送热
近年来,围绕隧道窑生产线的性价比,或者说到底应该建设哪种窑型,行业内产生了很大的争论,市场上基本也是百家争鸣、百花齐放。通过对多种原料、多种窑型多年跟踪研究,我们发现:影响隧道窑产量的主要因素可以归结为三点:原料特性、干燥工艺、焙烧控制。
原料的物理化学特性是内在的、固有的特性,生产线上的一切工艺流程都要围绕原料特点进行设计。干燥和培烧工艺是体现生产线先进性的核心工艺,干燥又是决定能耗和产量的关键环节,本文重点分析干燥工艺的原理和设计要点。
1 砖坯中水分来源及存在
砖坯中的水分来自于成型过程,不同成型工艺生产的砖坯含水率差别较大。实践中人们往往过分追求产量,降低了砖坯挤出压力,导致强度下降,砖坯含水率提高,还有的盲目码高,严重超出底层砖坯的承受能力,烧出的产品成品率很低。
根据实践经验,给出几类原料的成型含水率,供大家参考。其他类似的原料可以参考此数据。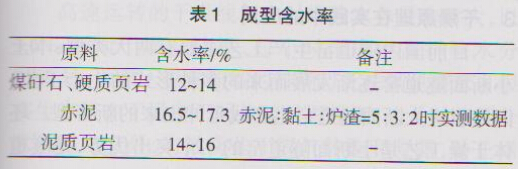
在允许的前提下应该寻求低含水率的成型工艺,能够保证砖坯码上窑车后不变形不开裂,底层砖坯能够承受住上层坯体的压力可视为合格。含水率越高往往干燥敏感性也会提高,干燥敏感性可以用公式表现如下:
K=(W1-W2)/W2)
式中W1——成型时的绝对水分(干基),%;
W2——干燥收缩停止时的绝对水分,%;
K——干燥敏感性指数。
K大时,干燥过程易出现开裂。显然,成型时的水分含量高,收缩停止时水分含量低的黏土对干燥敏感配料时应增加塑性低的煤矸石、煤灰、炉渣等原料使混合料瘦化。成型含水率也不是越低越好,过分追求低含水率会增加挤出难度,增加电耗,加快设备磨损。
坯体中的水主要是由三部分组成,自由水、吸附水和化学结合水。
自由水也叫机械水或游离水:分布在颗粒间和毛细管中,结合松弛,较易排除。自由水在干燥阶段排出。
吸附水:附着于颗粒表面,其数量与环境温度和湿度相关,并有一定的平衡关系,即随着周围介质条件可逆性变化。
化学结合水:包括在矿物的分子结构中,结合牢固,排除时需要较大能量。化学结合水含量较少,一般需要在焙烧窑的预热段排出。
在干燥条件固定的前提下,可以把坯体中的水分分为自由水分和平衡水分,在干燥阶段就要最大限度除去自由水分。
2 坯体干燥机理
在干燥室内,干燥介质(余热和热烟气)通过热交换将热量传给坯体表面,坯体表面受热后,又以传导方式将热传递给坯体内部,这是传热过程。坯体表面受热后,表面水分汽化蒸发,而坯体内部水分则因物料水分差而移向表面,再由表面蒸发,直到坯体得以干燥,这是质传过程。由此可见,整个干燥过程既是传热过程,又是传质过程。传质过程过程又可以分为两个过程,表面水分汽化蒸发到空气的过程称之为外扩散,内部水分移向表面的过程称之为内扩散。整个干燥过程中,传热过程、外扩散过程和内扩散过程是相互联系并同时进行的。在干燥介质的温度、湿度及流速不变的情况下,物料的温度、水分、干燥速度与时间的关系,如图一所示:
在干燥介质稳定,坯体不发生化学变化的情况下,坯体干燥可分为四个阶段:
2.1 升速阶段
干燥室内不停地有新车进入,在这个阶段,坯体表面被加热到等于干燥介质湿球温度的温度,水分蒸发速度很快增大,到A点后,坯体吸收的热量和蒸发水分耗去的热量相等。这一阶段时间短,排除水量不大,干燥介质温度最低、湿度最大。
2.2 等速干燥阶段
坯体表面蒸发的水分由内部向坯体表面源源不断补充,坯体表面总是保持湿润。这一阶段干燥速度不变,坯体表面温度保持不变,水分自由蒸发。干燥介质湿度逐渐增大。到B点(临界水分点)后,坯体内部水分扩散速度开始小于表面蒸发速度,坯体水分不能全部润湿表面,开始降速阶段,体积收缩不大。
2.3 降速干燥阶段
表面停止收缩,继续干燥仅增加坯体内部孔隙;
干燥速度下降,热能消耗下降,坯体表面温度提高。
2.4 平衡阶段
坯体表面水分达到平衡水分时,干燥速度为0。
干燥最终水分取决于干燥介质的温度和湿度。干燥各阶段并不是固定不变的,随着干燥介质温度、湿度的变化也会有所调整,实践中要根据具体情况摸索出适合原料特点的干燥曲线。
通过研究干燥机理及干燥速率可知,影响干燥速率的因素实质上就是影响传热速率和扩散速率的因素,其中,影响传热速率的因素为干燥介质的温度、湿度和流速,总体而言是送入干燥室内多少热量。热量可以用公式简单表达:
Q=T×C×V
式中 Q——热量,kJ;
T——介质温度,℃;
C——比热,kJ/kg·℃;
V——风量,m³/h。
在实践中经常出现这样的现象,有的生产线送进干燥室的热风温度较高,但是干燥速度就是很慢,干燥效果很差,这是因为风机抽取的风量偏少了,干燥室里并没有获得足够的热量。有的生产线送进干燥室的热风温度较高,但是干燥速度就是很慢,干燥效果很差,这是因为风机抽取的风量偏少了,干燥室里并没有获得足够的热量。有的生产线送风温度较低,但干燥效果却很好,这是因为风量较大,干燥室已获得足够的热量。一般情况下干燥室送热口温度在140℃~160℃比较合适,过高了会影响焙烧窑正常工作,也会使风机工作环境恶化,送风量应根据干燥室内需热量多少计算。
影响扩散速率的因素为坯体的温度、含水量和坯体的形状特征、坯体的颗粒级配。孔洞率大的砖坯比较容易干燥,砖坯暴露在空气中的面积越大越容易干燥。原料的颗粒级配也很重要,粗颗粒、瘠性料多的坯体,毛细管粗,内扩散阻力小而利于内扩散速度提高,有利于提高干燥速度,塑性高的原料,往往粒度愈细,成型时所吸附的水愈多,含水率大,不容易干燥,而且收缩与变形也大。含水率较髙原料干燥前后的内部显微结构见图2。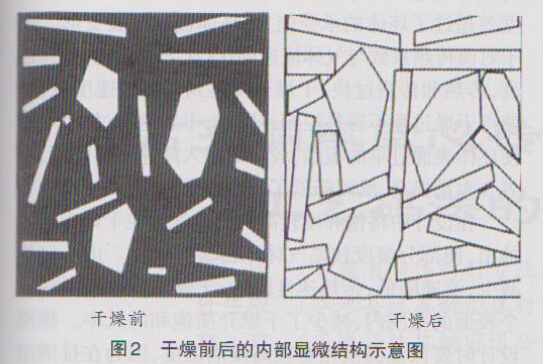
3 干燥原理在实践中的应用
目前国内隧道窑生产工艺主要有两大类型:本土小断面隧道窑逐渐发展而来的多种形式的生产工艺;国外引进大断面隧道窑生产线延伸出来的新窑型。坯体干燥工艺是小断面隧道窑的一个突出优势,是隧道窑高产的先决条件。这类生产线在干燥方面主要特点如下:
3.1 存坯线多
砖坯在室内静停时间越长,坯体含水率越低,大大减少了机械干燥压力。
某厂实际生产时,普通砖湿坯3.1kg/块,成型水分15%,干燥后残余水分3%,以此数据计算:每万块砖在干燥阶段需排出水分总量为:
3.1×[(15-3)/(100-3)] ×10000=3835(kg)
如果砖坯在进入干燥室之前能够蒸发成型湿坏中3%的水分,干燥室内排水量就变成了:
3.1×[(12-3)/(100-3)] ×10000=2876(kg)
每万块普通砖减少蒸发959kg水,相当于减少了1/4工作量,不仅提高了干燥效率,而且降低焙烧窑热耗。
3.2 干燥室长
高产生产线普遍干燥室较长,有的甚至建成多条干燥室配合一条隧道窑。适当延长干燥室长度便于干燥曲线调节,特别是干燥敏感性较强的原料适合经过一段低温预热阶段以防止干燥收缩。多条干燥室的设计充分利用了低温大风量的干燥原理。
3.3 余热利用率高
内燃烧砖工艺中能从冷却带抽出的热量小于外燃烧砖工艺,抽取预热段烟热补充干燥室,既提高了干燥室的送热温度又增加送风量,弥补干燥室热量不足的缺点,高产生产线大部分采用这种干燥工艺设计。
3.4 排潮能力强
高速运转的干燥线每小时排除水分量非常大,以3.6m断面干燥室计算,每小时干燥室需排除水分2500kg,单靠干燥室前端的排潮口无法满足要求。很多生产线在干燥室不同位置设置排潮口,及时将部分水汽排出室外,有效防止干燥气体饱和凝露,防止塌坯。
4 干燥室设计要点
很多4.6m、6.9m断面生产线在产量上不具有竞争优势,产量与3.6m等小断面窑炉相比,不能与断面同比例增加,很大一部分原因是干燥效率低下,砖坯进干燥室时含水率高,焙烧窑预热带只能当作干燥室用,降低了焙烧窑工作效率。在新生产线干燥工艺设计时要充分借鉴成熟经验,开发高效快速下燥新工艺。
4.1 适当增加静停时间
中大断面生产线投资较大,不可能无节制增加存坯线和窑车数量,但保证足够存坯线是必须的。我院新设计生产线存坯线一般要求存放24h以上,同时要求保证存坯线的温度,防止砖坯回潮。在有条件的生产线建立预干燥室也是一种尝试。邯郸马选砖厂所用煤矸石热值较高,我们在焙烧窑冷却段设计安装特制暖气管道,利用余热锅炉生产的热水为预干燥室供暖,极大地提高了砖坯干燥效率,提高生产线产量。
4.2 干燥室内通风设计合理
要保证窑车上所有砖坯都能干燥,就要确保干燥室内气氛均匀,尤其是在干燥室中后部必须保证是正压环境,为了确保一个断面内每一处的气体流速均匀,应控制砖坯与侧墙以及砖坯与窑顶间隙要小于坯垛间隙,我们设计干燥室顶间隙不大于5cm,侧墙间隙配合码窑方式,也依此数据为基数。设计码坯要求尽量增大砖坯迎风面积,砖坯间距兼顾边密中稀,坯垛整齐。
4.3 分段送热与多段排潮
干燥室送热与排潮设计直接影响坯体质量。干燥过程中,由于水分同时存在于干燥介质和坯体中,干燥介质中的水蒸气分压低于坯体表面的水蒸气分压,水分从坯体表面蒸发到干燥介质中。但是,如果干燥中出现了燥介质中的水蒸气分压高于坯体表面的水蒸气分压的情况,就会出现水分从干燥介质中凝结到坏体表由的过程,这就会引起返潮或塌坯。发生这种情况时,首先是干燥介质相对湿度很高,甚至已经饱和,其次是坯体表面相对干燥且温度低。在这样的情况下,干燥介质在传热给坯体的过程中,同时将水蒸气凝结到坯体表面,坯体吸湿潮解,强度下降,最严重的结果就是塌坯。因为冬天坏体温度相对较低,所以,塌坯在冬天容易发生,而很少在夏天发生。在干燥介质逆向流动的过程中,由于干燥介质温度大于坯体温度,热介质不断传热给坯体,在这个过程中,热介质温度不断降低,坯体蒸发的水分进人干燥介质,使空气的相对湿度逐渐升高,如果此时空气流速较大,传热传质速度很快,空气就很容易达到饱和。例如,某干燥阶段,干燥介质温度60℃相对湿度80%,即使不再吸湿,只是传热降温,当温度下降到55℃时,干燥介质已经饱和,干燥介质在继续逆向流动的过程中,传热吸湿同时进行,很可能在57℃~58℃时就已经饱和。因此,不恰当的使用提高干燥介质流速的方法提高干燥效率也有可能造成坯体坍塌。
在送风设计时要做到合理的提高干燥介质的湿度和流速。提高干燥效率的基本途径是在干燥敏感系数允许的前提下,降低介质的相对湿度,提高其温度、速度。干燥介质传给坯体的热量与干燥介质与坯体表面的温度差有关,提高介质温度就可以增加单位时间内介质传给坯体的能量,增加介质的流速,可提高对流传热系数,加快传热过程,从而提高传热速率。
但如果不合理地提高干燥介质的温度和流速,提高也可能造成干燥缺陷。在实际干燥过程中,如果温度差超过了坯体的承受能力,坯体极易开裂变形。由于对流传热系数与气体流速的0.8次方成正比,流速过高,传热和传质过快,干燥介质达到饱和的速度过快,使得干燥过程不容易控制。同时,干燥速率过大,可能使坯体表面过早的板结,较早的进入降速干燥阶段,临界含水量提高,反而降低了干燥效果。
在设计中将饱和度较高的部分气体在干燥中间段抽出,使部分湿度较高气体不再参与操作。由于气体减少,流速降低,传热速度降低,干燥流速被限制在一个较低的范围内,减少了干燥介质饱和的几率。排潮设计时要保证提供相对较高排潮温度,因为在排潮湿度一定的前提下,温度越高,需要空气量越小 温度下排除1kg水需要的干空气量见表2。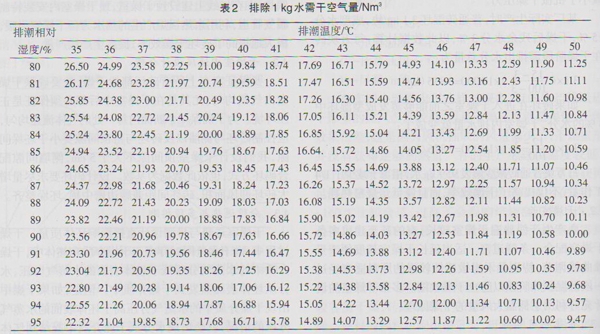
环美分院在多条6.9m断面干燥室设计中采用低压低温大风量分段送风工艺,干燥效果明显。采取多段排潮工艺时要注意脱硫系统设计,还要解决管道及风机防腐蚀问题。
5 结论
每种原料对干燥工艺要求不同,高塑性原料应掺加含有热值的低塑性原料作为瘦化剂,降低塑性同时降低干燥敏感性,尽量采用硬塑挤出工艺降低成型含水率。
干燥设计要在静停和机械干燥两个方面下功夫,充分利用隧道窑内富余热量最大限度干燥砖坯,减少焙烧密工作压力。
实践证明,合理解决干燥问题后,中大断面隧道窑产量可实现较大提高。
参考文献:
[1]黄烈武.人工干燥砖坯工艺若干技术调控(二)[J].砖瓦,2013(4).
[2]孙晋涛.硅酸盐工业热工基础[M],武汉理工大学出版社.1992(2).相关文章
- 2024-04-14菏泽市电力设备的一个强势品牌
- 2024-04-14电力电工解决方案的服务商
- 2024-04-14山东鸿盛电气科技有限公司
- 2024-04-09【鸿盛HONGSHENG,主要经营范围】
- 2024-04-09【鸿盛HONGSHENG,一个高端电力设备的品牌】
- 2024-04-09鸿盛电气的优势
- 2024-04-09鸿盛电气发展历程
- 2024-04-09鸿盛电气企业文化
- 2024-04-09鸿盛电气由“产品经营”走向“品牌经营”
- 2024-04-09鸿盛电气企业定位